Disruption! This is one word that manufacturers despise. They would like to avoid this in their day-to-daylife. The problem is that, while industrial staff dislike disruptions, do they plan and think ahead to avoid them? Alternatively, they leave it to "Chance".
There are numerous causes for disruptions. Today, we'll talk about how we may reduce interruptions byusing vibration measurement and analysis on industrial equipment. Large fans are one of the mostprevalent pieces of industrial equipment. Let us better comprehend the concept by utilising Centrifugalfans (HVAC) as an example.
Centrifugal fans, commonly known as blowers, are essential components of any HVAC system. This mechanical equipment is responsible for transferring enormous volumes of air from one location to another while maintaining comfort and air quality in a variety of commercial and industrial buildings. Centrifugal fans serve an important role in temperature regulation, making them essential components in both heating and cooling processes in the manufacturing industry.
By and large, the centrifugal fans are kept inside the Air Handling Unit (AHU) cabin. It is practically not possible to access the fan and assess the condition of the fan while it is in operation. It is a difficult task for any maintenance engineer to understand the parameters or symptoms of the fan, while it is in
operation. Hence there is a need to adopt a technology wherein we can predict the condition of the fan,well in advance, inside an AHU System.
It is of utmost importance to keep a high Uptime of this equipment. Machine / Equipment failures often occur due to continuous operation, sometimes over-use, and heavy cyclic loading situations. This process leads to the gradual wear of components, which increases the risk of failure. According to the IEEE, Industrial Engineering and Engineering Management, Maintenance costs account for 15% to 60% of the manufacturing cost of the final product. In heavy industry, these costs can be as high as 50% of the totalproduction cost. The said data varies from industry to Industry and the type of maintenance techniques being used. These costs & disruptions can be avoided by choosing an efficient maintenance strategy,which allows for detecting and correcting the problem in time.
The main objective of the maintenance strategy is to increase the availability or Uptime of machines, including Chillers, AHUs, and Compressors, keeping low, maintenance costs.
Let us first look at some Maintenance techniques:
These can be divided into three types
- Breakdown maintenance, (reactive)
- Preventive maintenance,
- Calendar-based Maintenance.
- Performance-Based Maintenance.
- Predictive maintenance (PdM).
- Calendar-based Maintenance.
- Performance-Based Maintenance.
Among the techniques used for equipment maintenance, PdM has proven to be the most efficient andeffective in the industrial environment. PdM is based on the analysis of data collected through monitoring or inspections. The data are collected from machines for example, AHU, Chiller, and Compressor, todetermine the health status and define the maintenance strategy.
Failures can be detected by a variety of diagnostic methods. Among the various techniques used inpredictive maintenance, vibration analysis has emerged as a valuable tool. The following fi gure explainsthe evolution of maintenance practices. How we began with reactive and now migrating towards new ioTtools and upgrading to CBM.
Next, let’s understand what Causes Vibration in a Centrifugal Fan?
• Unbalance in the rotating part, for example in large Blades
• Misalignment of couplings and bearings
• Bent shaft/ Worn, eccentric, or damaged gears
• Bad drive belts and drive chains
• Inaccuracies in bearings
• Electromagnetic forces/ Aerodynamic forces/ Hydraulic forces
• Looseness/ Rubbing and Resonance
This Vibration measurement & analysis technique has emerged as a powerful and well-established PdM technique for rotating equipment, commonly for Fans which are used in AHU, Chillers, and Pumps which are used in HVAC. It is a noninvasive and nondestructive method.
How a Vibration analysis can help in reducing the Life-Cycle cost of a centrifugal fan (Used in HVAC) and improves the longevity of the fan is partly explained in the table below.
Vibration Analysis Can be carried out by both “Offl ine” and “Online” Methods.
What exactly is Offline Vibration Analysis?
We know that Vibration monitoring devices measure the amplitude, frequency, or intensity of the vibrations emitted by any rotating piece of machinery, including motors, fans, pumps, etc. Every piece of rotating equipment has its vibration signature. A machine’s baseline, healthy vibration pattern can be determinedby taking a reading of the equipment when it is in optimal running condition.
Once the normal baseline is measured, maintenance teams can use either handheld vibration meters orvibration monitoring sensors affi xed to key points on the machine to measure the machine’s vibrationsover time. If the vibration pattern changes, it’s probably because there is a fault in the machine. Vibration monitoring can pick up on even minor defects in your machinery, giving your maintenance teams plenty oftime to make repairs before the problem worsens.
The data collection happens manually with the help of a hand-held vibration analyzer. To analyze the data and arrive at a solution and to implement the solution for the inaccuracies observed, we need the support of an expert.
What is “Online” Vibration Analysis?
Online Vibration monitoring is an effective condition monitoring tool where the sensors are mounted onthe bearing points of the asset permanently and are confi gured to collect vibration data on a real-timebasis. It can be programmed to provide alerts or alarms to users in case of any abnormal change in thepreset threshold values. To arrive at a solution based on the alerts, we need the support of a specialist inthe fi eld of Vibration analysis. Unlike offl ine monitoring systems, in Online monitoring systems, we cancapture the changes instantly.
Online vibration monitoring primarily starts with critical assets (Such as HVAC Equipment in a process plant), the expensive equipment that would contribute to substantial maintenance expenses, andproduction losses in the event of an equipment failure. Online continuous vibration monitoring is anessential tool to eliminate sudden breakdowns as it alerts the maintenance personnel of any minordefects at the very early stage providing enough time to perform corrective measures to eliminate thebreakdown. In industries, asset-wide online condition monitoring not only improves machine uptime, high productivity, efficiency, and reliability, but it also reduces life cycle costs. At a MNC plant near Pune, we have applied a set of sensors, which constantly provide data to the cloud. From there, we can review &analyze this data & predict ahead of a disruption hitting the customer. The curves generated are analysed for any anomaly.
Where to Choose Online vs Offline?
In rotating equipment like Air Handling Units (AHU), where the rotating equipment that is fan is mounted inside an enclosure, access to the equipment itself is a challenge, while the fan is running.
- Here we can adopt certain changes in the Offline vibration monitoring system
By say, mounting a permanent probe on the bearing
- Connect a cable to the probe and bring the other end of the cable outside the enclosure.
- This system comes with a limitation. As the length of the cable increases, the loss in signal to increases. Hence a site study becomes mandatory before adopting this modified mechanism.
Wireless online vibration motoring system, if adopted, although a failsafe system, comes with a highcapital cost.
In short, a “One Size Fits All” solution cannot be arrived at. On one end with the offline system, it has limitations in accessing the bearing points, and on the other end, with an online system, it comes with ahigh capital cost. Thus, if AHU or this fan is critical to operations, for example in a Paint Spray booth of an Automotive Plant, it is better to invest & keep high uptime, deploying online sensors.
On the other hand, if AHU is simply providing cooling air in some Plant, we can afford to deploy offline monitoring. To answer, “Where to choose what”, we thus need an inspection audit of the available equipment and application area and evaluate the technical feasibility of the Offline system. If the offline is completely ruled out, we need to go for an optimal method of the online system. The key to the success of a vibration analysis system depends on a critical evaluation of the equipment before investing.
By careful combinations, we can thus improve uptime or reduce “Disruptions”.
- By Sudhir Gurtoo, Managing Director and CEO, Leadec India & V Ramakrishnan
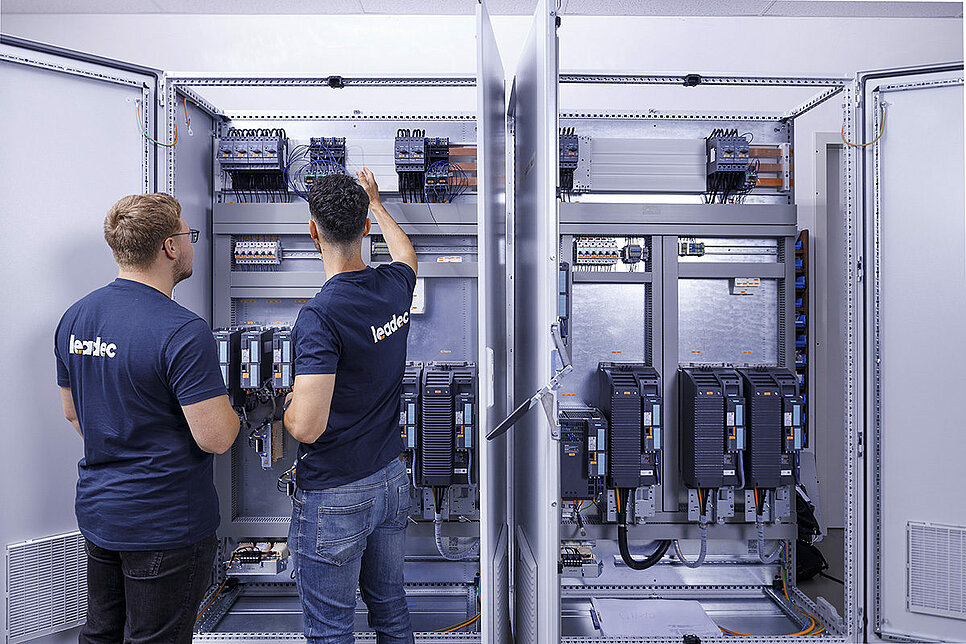